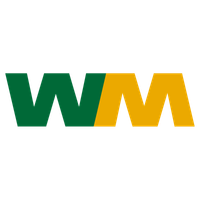
Waste Management Inc
NYSE:WM
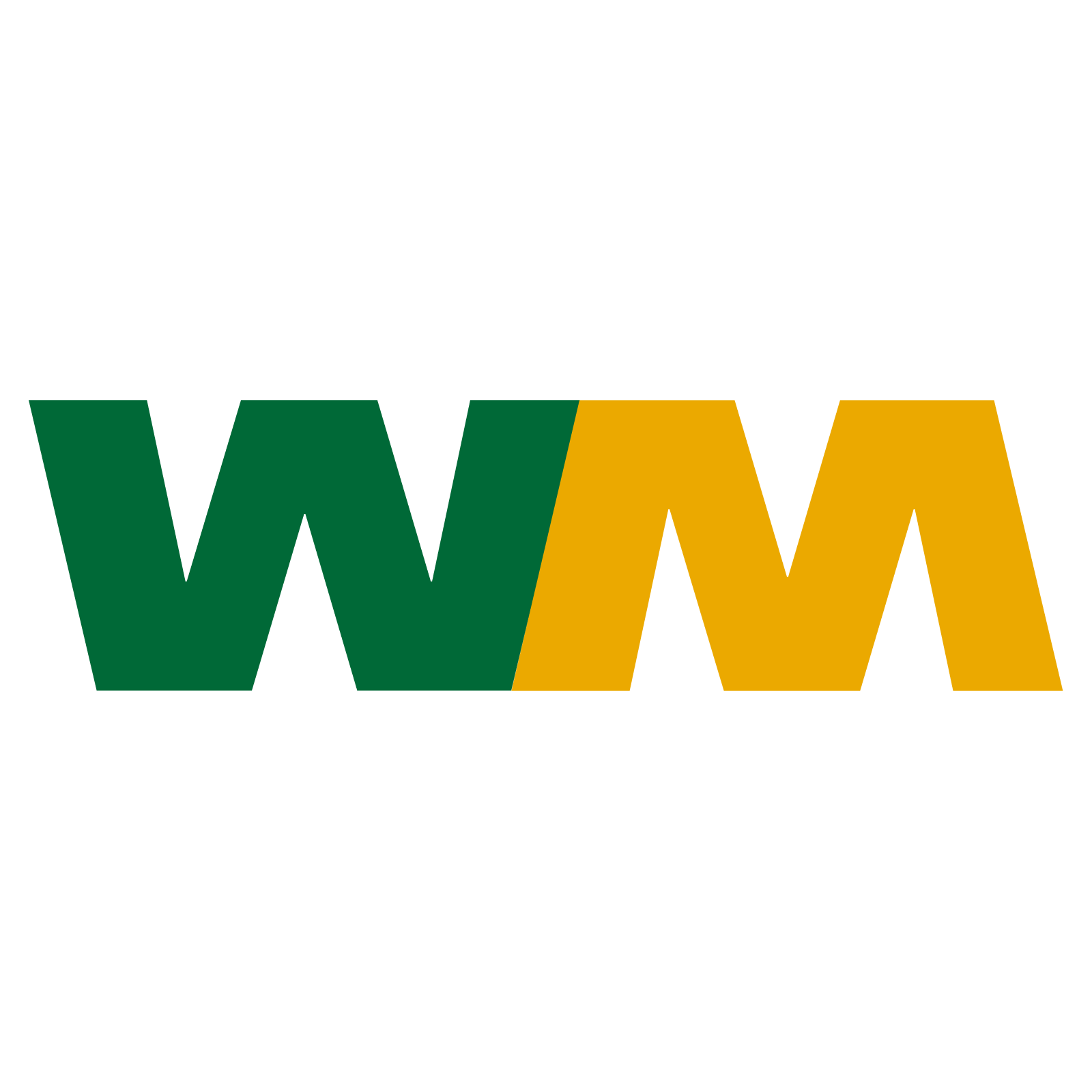
Utilize notes to systematically review your investment decisions. By reflecting on past outcomes, you can discern effective strategies and identify those that underperformed. This continuous feedback loop enables you to adapt and refine your approach, optimizing for future success.
Each note serves as a learning point, offering insights into your decision-making processes. Over time, you'll accumulate a personalized database of knowledge, enhancing your ability to make informed decisions quickly and effectively.
With a comprehensive record of your investment history at your fingertips, you can compare current opportunities against past experiences. This not only bolsters your confidence but also ensures that each decision is grounded in a well-documented rationale.
Do you really want to delete this note?
This action cannot be undone.
52 Week Range |
168.9802
225.68
|
Price Target |
|
We'll email you a reminder when the closing price reaches USD.
Choose the stock you wish to monitor with a price alert.
This alert will be permanently deleted.
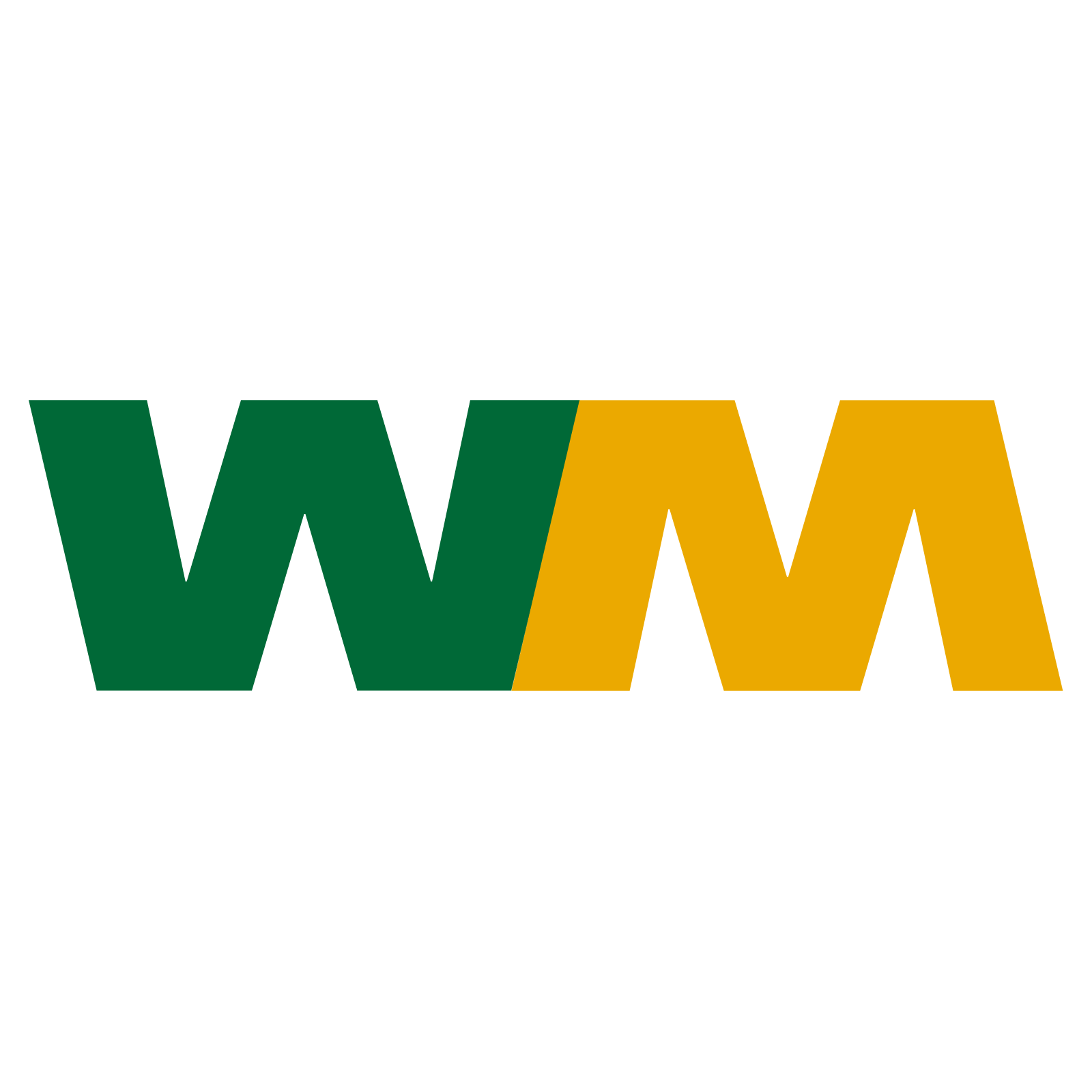
Thank you for standing by. Welcome to the Waste Management, Third Quarter 2021 earnings release conference call. At this time, all participants are in a listen-only mode. After the speaker's presentation there will be a question-and-answer session. [Operator instructions] Please be advised that today's conference is being recorded. [Operator instructions] I would now like to hand the conference over to Ed Egl. Thank you. Please go ahead.
Thank you, Erika. Good morning, everyone. And thank you for joining us for our Third Quarter of 2021 earnings conference call. With me this morning are Jim Fish, President and Chief Executive Officer. John Morris, Executive Vice President and Chief Operating Officer. And Devina Rankin, Executive Vice President and Chief Financial Officer. You will hear prepared comments from each of them today. Jim will cover high-level financials and provide a strategic update. John will cover an operating overview and Devina will cover the details of the financials. Before we get started, please note that we filed a Form 8-K this morning that includes the earnings press release and is available on our website at www. wm.com.
Form 8-K, the press release and the schedules of the press release include important information. during the call, you will hear Forward-looking statements which are based on current expectations, projections, or opinions about future periods. All Forward-looking statements are subject to risks and uncertainties that could cause actual results to differ materially. Some of these risks and uncertainties are discussed in today's press release, and in our filings of the SEC, including our most recent Form 10-K as updated by our subsequent Form 10-Q filings. John will discuss our results in areas of yield and volume, which unless stated otherwise, are more specifically references to internal revenue growth or IRG from yield or volume.
During the call, Jim, John and Devina will discuss operating EBITDA, which is income from operations before depreciation and amortization. Any comparisons unless otherwise stated, will be with the third quarter of 2020. Net Income, EPS, operating EBITDA and margin, operating expenses, and SG&A expense results have been adjusted to enhance comparability by excluding certain item that management believes do not reflect our fundamental business performance or results of operations. These adjusted measures, in addition to free cash flow are non-GAAP measures. Please refer to the earnings press release and tables which we found on the Company's website at www. wm.com, for reconciliations to the most comparable GAAP measures and additional information of our use of non-GAAP measures and non-GAAP projection.
This call is being recorded and will be available 24 hours a day beginning approximately 1:00 PM Eastern Time today, until 5:00 PM Eastern Time on November 9th. To hear a replay of the call over the Internet access the Waste Management website at www. wm.com. If you're a telephonic replay the call dial 855-859-2056, enter reservation code 6835518. Time-sensitive information provided during today's call, which is occurring on 10/26/2021, may no longer be accurate at the time of a replay. Any redistribution, retransmission, or rebroadcast of this call, at any form without the express written consent of Waste Management is prohibited. Now I will turn the call over to Waste managers, President and CEO, Jim Fish.
Thanks, Ed. Thank you all for joining us. Our third quarter performance highlighted the exceptional cash-generation capability of our business model as we generated nearly $1.2 billion of cash from operations. Our solid results put us on track to meet the higher full-year financial outlook we provided last quarter, even as we face some of the highest inflation that we've seen in years, along with the labor and supply chain constraints. Virtually, no segment of economy, including government and the private sector, has been unaffected by these historically accrued inflationary and supply chain challenges.
Disbursement inflation accelerated through the third quarter and during the quarter, we saw roughly $60 million of labor inflation at about $100 million of inflation in other operating cost categories. Overall, our underlying labor inflation for the third quarter was 8.7%. So that's the tough news. The good news is that the business continues to perform well as demonstrated by the fact that we still expect to finish the year within our previously adjusted operating EBITDA raise, adjusted operating EBITDA, and free cash flow guidance ranges. And we will be above our prior revenue range due to strong price execution and strengthening volumes. John, Devina, and I will discuss what we're doing about these labor and inflationary pressures in the short-term and medium-term.
Not surprisingly, our disciplined price programs are the primary lever to combat cost inflation. Our pricing programs delivered core price of 4.6% and collection and disposal yield of 3.5% in the third quarter. Standout performance continues to be the residential line of business with yield of 5%, while MSW yield improved to 3.5%. But keep in mind the price escalations on about 40% of our revenue are tied to an index, often based on a look back over the prior year. So, there's a timing lag in adjusting index pricing when cost step-up as quickly as they have. And it's important to understand that a portion of the remaining 60% of our business won't get the full 7% to 10% price increases we believe we need to cover rising costs, until their next price increase cycle. A customer who has increased 4% in May, won't get the full cost recovery price increase until next May.
That said, we're seeing a favorable price environment across our open-market businesses, evidenced by our low Let's level of rollbacks in more than a decade. We're very focused on directly addressing the labor challenges. John will discuss the quarterly impact and how we're working to address this immediately. Strategically, we're looking at this acute challenge as an opportunity to expedite the automation of certain jobs. We've said previously that we view the automation of certain high turnover positions as both a competitive advantage and a derisking mechanism in today's labor market where certain jobs simply don't attract the interest they previously did.
The most recent examples of that are the customer setup role which we just finished fully automating, and the 35-plus percent reduction in labor we've seen, where we've upgraded and rebuild our single-stream recycling plants. Given the success of these rebuilds and the labor inflation challenges of late, we have accelerated the retooling of the remaining singles-stream plans, and expect to address 90% of single-stream volume by the 2023-2024 timeframe. In the quarter, we saw some of the positive impacts of those new single-stream plans in our outstanding performance in our recycling business. Earnings contribution, and margins for recycling were at their highest level ever, driven by strong demand for recycle material and great operating performance from the new state-of-the-art [Indiscernible]. We were equally pleased with results in our renewable energy business in the quarter where robust growth continued, driven by more rents sales at higher prices.
With our long-standing expertise, continued growth and sustainability solutions and unrivaled asset network, WM is uniquely situated to support our current and prospective customers in their evolving sustainability needs. Our customers are increasingly seeking circular solutions for their materials, which is causing growing demand for recycled content. Of note, our focus on unlocking more plastic from the waste stream, drove a 25% increase in plastics we recycled since 2019. Recycling and renewable energy are 2 of our key growth areas, highlighted in our annual sustainability report published earlier this month.
The report outlines the progress WM has made against our sustainability goals, and details investments we've made to advance our sustainability journey. In particular, this year's report focuses on the people behind the progress WM has made in the past year, and how they are doing their parts to take care of our customers, neighbors, and the environment and communities across North America. The bottom line for the quarter is this, we generated higher-than-expected volume and revenue growth in the third quarter, which positions us well for 2022. At the same time, we faced an unexpectedly acute and fast-moving challenge from the inflation, supply chain, and labor shortage headwinds.
And we managed our way through it well and still expect to achieve results within our 2021 guidance ranges. And this challenge presents an opportunity for us to move more decisively in those strategic areas of automation, sustainability, and workforce planning to further separate ourselves in this industry. In conclusion, I'd like to thank the nearly 50,000 people [Indiscernible]. They continue to deliver driving another quarter of double-digit growth in revenue, operating EBITDA, and free cash flow. I'll now turn the call over to John to discuss our operational results for the quarter.
Thanks, Jim. And good morning. Our team continues to execute very well despite a challenging operating environment producing more than 7% percent organic revenue growth in collection and disposal business in the third quarter. This growth combined with continued integration of Advanced Disposal drove operating EBITDA more than 14% higher. As Jim mentioned, we are seeing pressure on labor and other cost categories, and we are addressing these impacts to our pricing programs to controllable cost management, efficiency improvements, and workforce planning.
Adjusted operating expenses as a percentage of revenue increased to a 180 basis points to 62.2% in the third quarter, as we experienced pressure from inflationary costs, supply chain constraints, and stronger-than-expected volume growth. In particular, costs-related to the hiring and training of new employees impacted labor costs in the third quarter. We also saw overtime hours increase as the team adjusted to meet the higher-than-expected collection volumes. We anticipated a good portion of this labor pressure that are showing up on our cost, as we made proactive market wage adjustments earlier in the year to get in front of labor shortages and meet growing demand. At the same time, we are working to automate a number of roles where we see longer-term challenges to attract and retain employees.
In the residential line of business, we continue to work through the last 40% of our route, including those from ADS that are not fully automated, while continuing to be very selective in the business we are willing to take on, as evidenced by our yield and volume results in the third quarter end of the last few years. While we are now incurring the cost associated with these investments, we're only in the early stages of seeing the benefits. Our labor market supply chain constraints that they accelerated in Q3, coupled with robust volume growth in the Third Quarter, have also added pressure in [Indiscernible] operations, repair and maintenance costs are increasing as we hire additional technicians and incur some overtime hours to address the strong volume growth, we continue to see in the collection lines of business.
Similarly, we've had to temporarily place some of our higher-cost trucks back in service to address the volume demands. In addition, our third-party sub-contractors, our transfer stations, are facing similar pressures and are passing those increased costs onto us. Overall, efficiency in the collection business in the third quarter, adjusting improved in the collection business in the third quarter adjusting for increased training hours. The fundamentals of our business remain strong and we are committed to recovering our cost increases through pricing and again, taking the most expensive truck off the road and reducing most expensive hour of the day. Now I want to focus on several of the positives in the quarter.
Turning to our strong revenue results, third-quarter collection and disposal volume grew by 3.8%, which outpaced our expectations. We continue to see strong volume driven by economic reopening with commercial volume up 4.6% and special waste volume up by 16.6%. And we see runway for continued solid performance in the fourth quarter. Customer metrics were also strong in the quarter. Service increase is outpaced, service decreases by more than twofold for the second consecutive quarter and churn was 8.7%. Year-to-date net new business for small and medium business customers is up more than 10%. Finally, our integration of advanced disposal continues to go smoothly.
We've combined around 70% of the acquired operations into our billing and operational systems and we remain on track to migrate virtually all the ADS customers by the end of the year. We have achieved nearly 26 million in annual run rate synergies during the third quarter, bringing the year-to-date total to $60 million combined with the $15 million of annual run rate synergies realized in the Fourth Quarter of 2020, we're on track to reach $100 million by the end of the year. And we continue to forecast another $50 million to be captured in 2022 and 2023 from a combination of costs and capital savings. Our teams are working tirelessly to provide safe and reliable service to our customers and communities, and I want to thank them all for their efforts. And with that, I'll turn the call over to Devina to discuss our financial results in further detail.
Thanks, John, and good morning, everyone. As we have seen all year, robust volume growth, strong recycling commodity prices, and an increased collection in disposal core price continued to deliver top-line growth ahead of expectations in the Third Quarter. As a result, we are once again updating our revenue outlook for the year. Total Company revenue growth is now expected to be between 17% and 17.5% with yield and volume in our collection and disposal business of about 6.5%. Its guidance also includes an expectation for continued strength in recycled commodity prices and RIN values. We're confirming our most recent 2021 adjusted operating EBITDA guidance, between $5 billion and $5.1 billion. Which is an increase from the prior year of about 17% at the midpoint, and almost seven -- almost 5% higher than our initial outlook for the year.
Third-quarter SG&A was 9.7% of revenue, a 40-basis point improvement over 2020. Included in our results is about $16 million of increased digital investments, as we advanced technology that will benefit customer engagement and lower our cost to serve over the long term. We remain focused on managing our controllable spending making sure that we allocate each dollar to initiatives that will enhance our business. Third Quarter net cash provided by operating activities was $1.18 billion, an increase of 15%. Cash from operations growth continues to be driven by our robust increase in operating EBITDA, including the contributions from the ADS acquisition and lower interest costs.
While there was a modest unfavorable working capital comparison in the third quarter, due in large part to the timing of cash from P&G credit and our deferral of payroll taxes in 2020. Overall, improvements in working capital demonstrate the benefit of tools we're putting in place to enhance our systems and processes. In the third quarter, capital spending was $464 million, bringing capital expenditures in the first 9 months of the year to 1.13 billion dollars. Our 2021 pace of capital spending has continued to be slower than we planned due to supply chain constraints and construction project or taking longer than planned.
As we discussed last quarter, we are proactively pulling forward capital investment, particularly in recycling, where we know the returns will be strong. Investments in recycling technology and equipment at our [Indiscernible] are expected to be about $200 million for the year. While we continue to target full-year capital spending at the low end of our $1.78 to $1.88 billion guidance range, we could see 2021 coming in below targeted levels with some of our spending pushed into 2022 primarily due to supply chain constraints. We generated $773 million of free cash flow in the Third Quarter. And through September, our business generated free cash flow of $2.29 billion, putting us well on our way to our full-year targeted free cash flow of $2.5-2.6 billion. We've returned more than $1.7 billion to our shareholders through the first nine months, paying $730 million in dividends and repurchasing one billion dollars of our stock.
We continue to expect to repurchase up to our full authorization of $1.35 billion in 2021. Our leverage ratio at the end of the quarter was 2.71 times, as the strength of our business performance in the successful integration of the acquired ADS business, drove the achievement of our targeted leverage ratio ahead of plan. As we enter the final stretch of 2021, our teams are focused on accelerating our disciplined pricing programs, managing our controllable costs, positioning WM as an employer of choice, and capturing growing volumes. We know our strategies set this up for a solid finish to 2021. With that Erica, we'd be happy to address the teams’ questions.
As a reminder, to ask a question you will need to [Operator Instructions]. Your first question comes from the line of Tyler Brown with Raymond James.
Good morning, guys.
Good morning, Tyler.
Hey Jim. Thanks for all the color on inflation. I know you guys don't give a ton looking ahead on these Q3 calls, but it just sounds like the setup for pricing looks very favorable next year. I mean, you've got clearly this inflationary environment. You have strong CPI resets and you alluded to an open market that let's just say feels very rational. So just big picture. Why wouldn't pricing in '22 accelerate pretty meaningfully? And do you have confidence that you can price in excess of unit cost inflation next year?
Yes, I think you're right about that, Tyler. I think that's probably the single biggest message of the day, which is this, yes, we saw some cost inflation, which has been talked about at any business show you watch on TV talks about it, and add a little bit of -- it was a quicker than we thought. It was more acute than we thought. And the price that is our biggest lever, as I said in my remarks. To offset that, is not perfectly timed with that. So, there is a lag there. We've talked a lot about the fact that 40% of our business is tied to an index. And I mentioned that there is a, in many cases, a look back on that. About title rep, 40% of our business in that 40%, about 40% of that comes in January.
So, the price adjustment comes in January, about 30% comes in July, so 70% of the price increases on that index business come in the first half of 2022. And then the remaining 30% some of it comes in October and then there's a spattering that comes in the remainder of the year. And then on the open market piece, I gave the example of the customer that -- the job the 4% price increase back in May. And we still have a customer to keep in mind here. We don't want to go back to those customers and, hey, inflation hit us hard than we thought, so we're going to go ahead and increase you buy another 6 here in October. We're going to be smart about it and wait until we get to their annual cycle, in May of next year, and then we'll increase them by the amount that we need to cover costs and improved margins.
Yes. Okay. That is extremely helpful. Real quickly, Devina. So, it sounds like there's a lot going on in the EBITDA margins this quarter year-to-year. I don't know if you can distill it down, but can you just help us bridge out that 140 basis points down in EBITDA margin, specifically, and some of the key buckets there?
The two primary buckets to look at are really the inflation impacts that we've discussed and then recycling brokerage. So, we would say that about 60% of the impact was from inflation and about 40% was from recycling brokerage. To put a little more color around the inflationary impacts that Jim mentioned earlier, that total was a $160 million during the quarter, we estimate that our normal inflationary impacts would have been about 60 of that. So that was a $100 million in excess of what we consider normal inflationary impact.
And then, you might recall that we had projected that we were going to have about 60 million over and above our normal run rate in the back half of the year. So, we think that our costs in Q3 were about $60-$70 million above what we would have projected, and that you can see is a pretty meaningful impact to the overall margin of the business. I think it's important to look at our cost structure and see that 35% of our operating costs are labor-driven. And then when you consider subcontractor costs, which is effectively indirect labor, that's another 15%. 50% of our cost structure is labor-driven and we've seen that as a big driver.
And Tyler, I would only add that, with the additional volume I commented on in my prepared remarks, part of what we've done is we're spending a little bit more overtime in the short term to be able to go out of service and take advantage of the strong volumes. I mentioned in my comments that outpaced our expectations, which we view as a good thing over the long term. And certainly, we have a clear line of sight to what those costs are as Devina spoke to.
Great. I'll hop back in the queue. Thanks.
Thanks, Tyler.
Your next question comes from the line of Hamzah Mazari with Jefferies.
Good morning. Thank you. Just a follow-up on just operating leverage. I guess listening to your comments, is it fair to say that second half next year is when you'll see greater op leverage? Just given timing of these pricing resets and related to the op leverage, how much of your cost increase is incremental hiring because of labor availability issues impacting that, versus how much is just restarting your existing labor cost base up that you referenced with wage adjustments? I would also put subcontractor cost into that existing labor reset, I guess.
Yes, Hamzah, good morning. I would tell you that when I look at the labor increase hold hours and this is in aggregate. About a quarter of it is related to some additional training and hiring we're doing, some of that has to do with turnover pressures that I think we're seeing, and just about everybody in a transportation industry is seeing. I think the good news is, over the last four or five months, we've actually started to make good progress in terms of our retention rates on whatnot. And I think the labor resets we talked to last quarter, which are clearly showing up in this quarter as well, are having an impact there.
The other three quarters of it, if you will, were up numbers is related to some of the OT we're incurring. Part of that, as I mentioned, is we don't view that over the long term as a bad thing because we're seeing volume increase as we are outpacing our expectations. I think as Jim mentioned previously to Tyler's question, we have a clear line of sight on what we need to do through pricing and efficiency gains, etc., and automation to be able to overcome that. I do think 70% of that index, business resetting in the first half of the year is clearly something that we're focused on, and as Jim mentioned, our pricing strategy more broadly is not going to change, our expectations will have to change to keep pace with the cost increases we've outlined.
Got it. Very helpful. My follow-up question I will turn it over is, just around investment in automation, as well as technology, could you -- and I know Jim, you referenced the automation peace being accelerated and you mentioned the Murphs and you mentioned automation of some customers start up functions. Maybe at a high level, what inning are you in terms of automation, what, is there left to do? And is it just on recycling? And then also as part of that, just from a technology perspective, again, what's behind you? What's yet to come? Thank you.
I think comps that we're probably in the second inning, I like using the baseball analogy since we're in Houston today, but I think we're probably in the second inning here. There's a lot that falls under that automation umbrella. It's not just -- we've talked a lot about customer service digitalization, which is really is kind of the digital side of that. But the automation that I refer to is -- while it's technology, it's not technology as we think about it. It's not your mobile device. It's optical sorters at our plants. And we have 45, I think, single-stream plants. And we've fully automated 4 of those plants at this point.
So, if you think about the fact that we're taking 35 - ish percent of labor out, and to put that into dollars for you, it's about a million dollars per plant per month in labor savings. And think about the fact that we still have 40 of those plants -- 40 - ish of those plants left. Now, some of those plants, we're obviously automating the big ones first, so you won't get a million dollars from the very smallest plant, but that's a piece of the automation. But to your question, it's not just those recycled positions I mean, we have a lot of positions that have very high turnover that feel like they lend themselves to automation and we'll be looking at those going forward.
So, what's the total number that would be impacted by [Indiscernible]? But I think it's certainly more than just customer setup, which we fully automated and recycling. And then also, I want to make one last point to your question to John on OpEx, which we haven't talked about, but if you think about the COVID effect, we had almost 900 employees out at the peak. And the peak week I think, was the third of September. And we pay those employees, we made a conscious decision to pay them. If you think about the impact of that 900, by the way, a lot of those, probably over half of those were drivers. so, we are paying them and at same time, we are picking up their routes with overtime hours.
The cost of that was somewhere between 2 and 3 million bucks over a two-week period. So, it's not insignificant. And that number of both, that 900 by the way is quarantined employees and COVID employees. Employees who have the virus. That number has come back down as we've seen it across the U.S. to a much more manageable number it's in the -- I looked at the essay it's in the 200 range now down from the P. So that was a short-term cost that we were bearing. That was certainly coming back and we won't see that repeat unless we have another variant that kicks off and causes us to be back in the same position.
Still, I just want to clarify one thing, the savings from the recycling plant is a million dollars per plant for quarter, not for both?
Sorry. Sorry. I knew it.
Got it. Thank you so much.
Your next question comes from the line of Walter Spracklin with RBC Capital Markets.
Good morning, everyone. Thanks for taking my question. So, press assistance for Devina, looking at merging enhancement in and you've had a great track record in historic years of achieving margin, margin improvement year-to-year, but now, as you re-priced and a lot of your re-pricing is to pass through costs, you are able to protect EBITDA dollars, but it can be somewhat margin dilutive given the pass-through nature. So, when we look to next year, is there any cautionary you're cautioning us to keep that in mind when we look at historic margin expansion versus next year margin expansion, given that a lot of your revenue is cost pass-through revenue though.
Yes. I would say that, what's really important is to go back to one of Jim's earlier comments about the fact that, the acute nature of the cost increase that we experienced during the third quarter. And the fact that our index revenue is more significantly weighted towards the first half of the year, indicates that we had a mismatch in terms of when a lot of those price increases are pushed through. And when we experienced the more acute cost increases, we are not in any way indicating that this is anything other than that lag and kind of a one time or short term, I should say, impact in terms of margin.
Degradation, our outlook remains strong in terms of the businesses ability to work, both through pricing and operating efficiencies as the automation that we've discussed in order to improve the long-term margin of the business. I think that 2022 can have some noise in it with regard to some of these timing differences continuing, particularly as you think about the year-on-year impact of the volume expansion that we've seen in 2021. But our outlook remains solid with respect to expectations over the long term being one of margin expansion even with a higher cost structure.
Okay. That's great color. Appreciate that. And then my follow-up is just with regard to wages and the percentage of your workforce that has been re-priced if you want to call it that, is there a larger part or a meaningful part of your workforce that you perhaps are coming up on wage discussions or renewal that will likely see an outsized price increase that has not yet been built into your numbers, or are you pretty much done it from that overall wage repricing type of framework?
So, Walter, most of the wage adjustments we spoke to in Q2 and have carried through in Q3 have really been in drivers, technicians, front-line employees, our recycling folks, etc. So, I'm taking the swag here, but it's probably 2/3 to 70% of our folks have -- are in that population in some way, shape, or form. And Greg, that's not to mention -- say that we've raised rates on every one of those employees, but we've addressed that employee group. And then the balance listen, I think everybody's in a competitive labor market right now. We're keeping a close eye on the other 30% to 35% were part of that initial push. But that's something we do on regular basis and we go through that at least annually to make sure that we're compensating all's folks adequately relative to what's going on in the market.
Okay, that makes a lot of sense. I appreciate the time as always.
Thank you, Walter.
Your next question comes from the line of Michael Hoffman with Stifle.
Good morning. 2018 solved a lot of the inflation for the first time, the market's first-time seeing garbage deal with inflation. How would you compare the pace of that versus the pace of what you're experiencing right now? And then let's remind everybody, you covered all of that inflation with pricing, eventually then too.
I don't think they're that close. I think this is this is far more acute than what we've seen. I'm not sure there's anybody working at our Company today. Maybe a couple of people in their '70s that have seen this type of rapid inflation. At the example I gave of the customer that got the 4% price increase in May was a real example. So, we weren't even seeing this in May, this came on as quickly as almost the end of July but -- and really has accelerated. You weren't hearing people talking about it.
I mean, it's being talked about all the way up at the White House, being talked about by the Fed s Chair so I would tell you that this is more acute than we've seen before, but the other thing -- and you're right Michael, we did cover it with price and we think price is the primary labor to cover this and we're doing a good job with it. But it's why I wanted to make sure we stressed that there are some high turnover jobs that really don't have to do with this inflationary period.
There are some high turnover jobs that we need to really serious look at automating, and at the same time using customer service digitalization to really extract maximum efficiency out of our organization. John and I have talked a lot about it, and we think when we fully automate these routes, there's somewhere between 10% and 15% efficiency improvement, because you're not going to automate a truck driver job, certainly in my career, maybe even in my lifetime. But we do think we've got significant opportunity there on the driver side for efficiency growth.
Okay. Fair enough. So clear message is, and you've said this in pieces, but I want to say it out loud, you've expected to cover all this inflation. You just need time and time isn't years, it's months.
I think that's right. I mean, the 40% -- I think we should focus on the 40%. That is indexed driven and then I talked about, how half of that or 70% of it happened in the first half of the year. There is a look-back, so the adjustment that comes in January for some of those big contracts, some of those have a 12-month look-back which won't capture the full effects of inflation. We wouldn't get the full effect of this last three months of inflation on those adjustments. We wouldn't get the full effect of that until the adjustment we take in January of 2023. The adjustments that we take in July will pretty much reflect all of the inflationary -- this acute inflationary impact.
Okay, fair enough. Devina, on the free cash flow, what are your assumptions to maintain the guidance of 2.5 to 2.6 on cash flow from ops and capital spending?
From a capital spending perspective, we would love to spend every bit of the full-year guidance that we put forth the $1.78 to $1.88 billion. But as I mentioned, all year we've seen things move just a little more slowly than we would've liked, and we have taken some proactive steps in order to pull some capital forward. That being said, right now, we think we could finish the year somewhere in the range of $1.7 to $1.8 billion. We'd love for it to be a higher number than that, particularly as we've made investments in renewable energy and recycling specifically. In terms of the other puts and takes, I think is important to recall that we expected an increase in our cash taxes on a year-over-year basis.
We've seen that through the 9 months, but you'll have another leg of that in Q4. And then we've seen significant working capital contributions in the first 9 months of the year. We think we'll give some of that back in Q4, just based on some of the timing impacts of some payments that we have. But all-in-all really good performance in cash flow for the year, I would say it is the one that has certainly exceeded the expectation in every single aspect of contribution. All in all, total free cash flow at about the midpoint of 255 is tremendous growth. On a year-over-year basis and meaningfully ahead of the 1965 that we normalized, when you look at 2020 for the impact of the proceeds from divestitures from the ADS transactions. So that shows the level of growth on a year-over-year basis and free cash flow.
Okay. But to sum your comments, if you end up spending on the lower end of Capex, there's an upward bias to the midpoint of the range on free cash flow.
The one thing I would caution there is on the cash flow from ops we do have the taxes and working capital impacts that I mentioned. That's the only caveat that I would have there, but yes.
Okay. And then John, I saw Tim Hawkins and Jason Kraft and a couple others from other companies recently, they were all in a NWEA meeting and they all suggested that peak open positions -- you had past peak open positions and you were at least no longer struggling against peak open. Is that an accurate statement still? So, this pressure has peaked and started to add a little bit?
I would tell you within WM, as I mentioned in my prepared comments, probably last 4 or 5 months, Michael, we've really started to show some progress in terms of being able to net add, if you will, month-in and month-out at some of those key positions, specifically, the driver ranks. There's still a lot of competition out there, there's still a lot of pressure, as Jim mentioned, you can't turn on the TV without hearing about some form of pressure and transportation, whether it's marine, whether it's rail or whether it's truck transportation. But as I mentioned, the good news is I think the efforts we made to make some of those wage adjustments coupled with our efforts around retention and hiring are certainly yielding positive results here for the last 4 or 5 months.
So, you're off the peak open positions is the clear message?
Correct.
Michael, think about it, we have 10% - ish of our drivers that are making over 100,000 a year. And I don't know what the figure is for 90,000 above, but it's significantly higher than that. So, at the same time, we have really good benefits, we've announced the education benefits several months back. We chose to pay them during COVID, we've chosen to pay them -- still paying them when they're out on quarantine. We really have focused on taking care of our teammates here and we think that pays dividends for us in terms of reducing the amount of churn.
To John 's point, I think the number I read last week was, there are 82 thousand open trucking positions across the U.S. And then of course the same time we're seeing this volume increase. And so, we're trying to compensate for that as well. It's a good thing, it's a good problem to have, but yes, to John's point, we're getting past that peak but we think we're well-positioned. We like our [Indiscernible] these roles as part of why we're -- we have really good pay benefits and we hope to make sure that we differentiate ourselves there.
And then last one for me, for John, I think I picked up in your remarks, [Indiscernible] are seeing net new business growth not just where you opened leverage. Its net new business growth and there's momentum, that momentum should continue. So that's good news, but I guess there's two pieces to that. How does that impact the thoughts about capital spending inflation be able to meet that net new business growth.
Well, first I would tell you 2 things I mentioned on our prepared remarks, Michael, which are pretty familiar to you, which is the net service increases versus decreases is strong from Q2 to Q3. And then I mentioned also small and medium business, which is a traditional collection business and that I would say temporal off and the big really large accounts. We're seeing good momentum there. That was the 10% number, but I don't see in terms of capital, I mean, the capital spends there would be some incremental capital, containers and to some extent, when you guys -- we've talked about before that step function between filling up a raft and the next raft, but we don't see that as out of the ordinary capital spend.
Terrific. Thank you very much.
Next question is from the line of Kevin Chiang with CIBC.
Good morning, everybody, thanks for taking my question here. If I can ask us on your repricing strategy for next year, just given how acute inflation as you've mentioned, Jim. Just wondering how you look to maybe limit or you've got lag between when you see pricing versus maybe this year that inflation might be more persistent than we all had hoped a few months ago. But like, are you looking at contract terms that might allow you to reprice in the event that inflation continues to persist at elevated level? Or are you pricing for maybe what do you think inflation could go versus maybe, what costs you've seen increase in the back half of this. Just being interested in seeing how you think about that repricing strategy to kind of limit that lag, as you look out into 2022.
Yeah, Kevin, the lag really just hits us in the first part where we're this kind of three-month period, once we catch up with that, and once we catch up with these adjustments on the 40% that's index-based then, unless inflation runs up from here, which we don't anticipate, I'm not sure I've seen anybody that anticipates that, then we feel like we're in a really good position with pricing to cover these cost increases plus add the margin. Now if inflation goes to 15% then I will retract that statement, but I don't think anybody expects that, so right now, if you look at core price, for example, we're pretty happy with the core price numbers that we were showing. Core price was 6.1% for the quarter in commercial. That's a big core price number if you look at the landfill line of business which has gotten a lot of questions over the last couple of years.
Core price in landfill was 4.6% as 2 consecutive quarters over 4% of core price. And really that's probably the best metric for looking at price increases, is core price versus yield. Yield was very good as well, but the core price probably is the best approximator of price increases. So, I feel really comfortable with the existing CPI and core inflation in the system that the pricing mechanisms that we have in place will cover that and also provide us some opportunity to improve margins as we go into 2022. keep in mind that 12-month look back, a big piece of the adjustment that's coming in January won't include all of the inflation that's going to take a year to capture that.
That's great color. Yes, let's all hope we're not heading for 15% inflation there. Maybe I can ask a non-inflation question. Recently put out this P-fast strategic roadmap, I guess as it looks to evaluate what the studies and I guess things they look to go over the next few years. Just wondering, as you look at the roadmap that you put out there, is there anything that you would comment on? Does it align with what you thought that EPA would do? Or think the EPA should do as they evaluate the P - fast strategy?
Yeah. Kevin that was just something off the press here in the last week or two with some milestone dates that the EPA published on some things they want to get covered, but I think that our answer is still the same to that. It could present a little bit of short-term cost impact to us, but we still believe over the long term, the post-collection assets we have are going to benefit from that certainly over the long term.
All right. I'll leave it there, thank you for taking my questions.
Thank you.
Your next question is from the line of Sean Eastman with KeyBanc Capital Markets.
Hi, Jim. Thanks for taking my questions. I'm just curious if you've seen any instances where this labor shortage is causing a down take in service quality. Have you guys track that anything concerning there? I just wonder if that ultimately impacts WM's ability to continue this great pricing trend we've been seeing?
So, Sean, there's pockets of it. I mean, first and foremost, we track it, we track it everywhere every day. And all of us get to keep a close eye on that. We have seen some pockets of pressure for sure where we've had some acute turnover issues. But as we mentioned in Michael -- to the response to Michael's question, we feel like we're past the peak and we're making headway there.
To your second question, is it profound enough for us to have to concede anything on the pricing front? No, we don't think so. And I think if you look at where a lot of the -- probably with the most acute labor issue was, for us is really around if you look at our residential, and you look at our pricing -- what our pricing strategy has been and what our corporates and yield results were for the quarter and over the last number of quarters, it has not impacted us there or frankly, in any other line of business.
Well, I think it's on the churns. The churn is probably the best metric for us to gauge that. And churn came in at 8.7% for the quarter. We look at the same quarter prior year was 8.8%. We're not seeing an uptake in churn, I think we're doing everything we can at the operating level, there's a lot of pressure on the operation, when you have 500 - ish drivers out due to COVID during the peak or when we've got all of these hiring pressures, you expect that there's going to be some pockets, as John mentioned.
And we're doing everything we can to make sure all the way up to my level. I get notes from customers saying, hey, my recycling was missed today, and so I pour that out to the right person to make sure that we pick them. But there have been some pressures, but we think that we're moving in the right direction and it certainly helps when you see that number of 900 employees out for COVID come down to 200. That was a pressure that was hard to compensate for.
Okay. That's helpful. And what about safety? I mean, do we need to be kind of incrementally concerned about safety and the costs associated with safety issues around this labor dynamic. What's the thought there, Jim?
Well, I should probably let John answer that but the answer would be we never compromise on safety. Safety is at the very top of our list. And so, we are extremely focused on being a safe organization. John, anything to add there?
Well, I would tell you that's where --that's one spot where technology and to some extent automations are helping. We're in the process of updating all the on-board equipment for our collection vehicles, our supervisory vehicles, with regard to being able to scan what's going on with behavioral issues, so we've got some artificial intelligence has been -- is about 70% through our entire collection fleet. They will help with things like following distance, cell phone usage, that kind of thing.
So no, I think if you look at our safety results, we've seen a little bit of pressure as we have integrated ADS, but the core WM business continues to perform well, and we're well on our way to getting ADS. The ADS business, totally tucked-in there as well. It's part of why we saw a doubling of our training hours because as we're hiring more folks, we absolutely make sure that they get fully trained. And so, we saw that 2x in our training hours, we think that number comes down as we're hiring fewer and fewer drivers and technicians.
Okay. Very interesting stuff. Thanks for the help guys.
Your next question is from the line of Noah Kaye with Oppenheimer.
Thanks for taking the question, and frankly, I know I can do as a reminder not to use my cellphone when I'm off the road, so appreciate that guys. I guess the linkage between potential Capex shortfall in operations is something I'd be interested to learn a bit about. Obviously, the commercial vehicle industry's experiencing production constraints, and that's impacting customer delivery. Just wondering how is this impacting the cost structure? I think you mentioned having utilized some older vehicles, but maybe you can talk through a little bit how that might be translate into elevated [Indiscernible] this year.
Sure, now. I think the way that we think about that, John mentioned, having to take some of the older vehicles off of the sidelines, so to speak, and pull those into service. We saw that most significantly in the industrial line of business and roll-off, because that's where we were able to flex most significantly in 2020. While we do see it on the operating expense side, our long-term focus continues to be on optimizing our fleet strategies so that we focus on reducing the total cost of ownership of each vehicle. We have seen some pressure in terms of per unit cost on the fleet overall. Some of that general inflationary cost pressures, but some of that is that we're driving towards automation to the points they've made earlier particularly in the residential line of business.
So, while we have a more expensive unit on the street, we definitely see the benefits of that in terms of lower operating expense both from labor and efficiency. So overall in the current quarter, that's a component of the cost pressure that we saw. But I would say that that was certainly secondary to the wage pressures that we experienced overall and we expect that to abate as we get truck deliveries. It's an interesting point that through nine months, we'd only gotten 70% of the trucks that we expected to get in 2021 to date. So, we think that when we get those trucks delivered, you'll start to see some of those impacts reduced as well.
That's helpful. I guess, on the flip side of that, there is what I presume are industry-wide labor and others shortages to do construction work at landfills for expansion. Presumably that's going to be a source of upward pricing pressure at the landfill. You had 3.5% yield this quarter, but I assume you got a pretty robust pricing outlook at the landfill. And this may be a contributing factor.
Yes, I think Jim did a good job of categorizing some of that too. I think there's a few places, steel costs, container costs, or [Indiscernible] landfill liner, those are all things that our supply chain team and the respective operating teams are keeping a close eye on. And we may make a decision to a fixed can versus buy-one while steels up 200% or whatever the number is. But that's not the bulk of it. I think Devina spoke to the majority of which is really a fleet spend some of the delays there coupled against strong volume. So that's why you talked about some of this cost pressure being somewhat acute not having confidence whether it's on a collection or the post-collection side, including the transfer of subcontractor side that we're going to be able to recover that.
One thing really quick, Noah, that I would caution against is matching the price increase that we got on third-party volume at the landfill against what might be our cost increase there. That doesn't -- by the way just because we got 3.6% yield, I think was the number. So, 3.5% yield on MSW, that does not imply that that's what our cost increase was at the landfills. Keep in mind a lot of the volume that comes in a landfill is our own volume which gets priced at the curve, which gets priced at the street. So, our overall, we've talked a lot about our overall cost increase. That includes cost increases that we're seeing at the landfills and I wouldn't necessarily assume that just because we got 3.5% on MSW, that that means that's landfill prices are costs are only going up by 3.5%.
Appreciate that. Thanks, Jim and John. Devina, maybe just one quick one. Any one-time or pull-forward of spending programs that you're currently doing this year that could turn into a margin tailwind next year as you lap, I know that customer service digitalization has been investment focused, but anything you would call out that sort of a margin tailwind next year, that's controllable?
The only one that we've mentioned over the course this year that's higher and therefore creating some margin compression in 2021, is our incentive compensation. That being said, I think everyone at WM would love to see us knock it out of the park next year such that that's not a giveback in 2022, but it's the one that I would call out. There's not anything else other than inflationary lag that we've already discussed.
Perfect thanks so much.
Quit texting and driving Noah.
You got it.
Your next question is from the line of David Manthey with Baird.
Thank you. Good morning. Tagging onto that last question, I believe in the past you've said about 15% of your labor unrelated benefits component of the cost stack is over time. And you noted it was elevated this quarter. Can you give us an idea of how elevated it was relative to that long run average. And then, should we expect that to normalize into next year as COVID settles out and hopefully you get in front of some of these labor issues.
No David, I think overtime was up about 6% for the quarter. and yes, I do think that as we get some of these folks on board, that we've talked about it from our staffing efforts, you're going to start to see, as I mentioned in prepared remarks, take the most expensive outlaw off the street and right now, because of some of the staffing challenges, but also because we've got volume in the collection lines of business particularly commercial and industrial that really outpaced our expectations. We view that as a good problem to have long-term and the short-term, obviously we're spending a little bit some premium dollars to get that volume collected.
So, one quick clarification because it's a great point, David, and this 6% increase is actually on a sequential basis when you look at that on a year-over-year basis, it is meaningfully more pronounced. Their year-over-year is about 30% increase in overtime hours that you saw in our costs in the current year.
Right. It was down significantly last year, so I guess it would've been up anyway, right?
That's right.
[inaudible 00:57:00] up year over year.
It is up year over year cost and ba -- we were already seeing some of that in the second quarter so the sequential impact is meaningfully lower.
Okay. Thank you. And just a dumb mechanical question here. Can you help me understand the mechanism by which higher recycled commodity prices drive your operating expenses higher?
Sure. In our operating expense table and as you will see what we call a cost of goods sold line. And that cost of goods sold line is where our rebates to our customers show up for the higher commodity prices. We also provide a table in the press release that shows the impact of that on margin and the current quarter that was 140 basis points. So, a very significant impact to the year-over-year comparison
Makes sense. Thanks very much for that.
Okay. Thank you.
Your next question comes from the line of Jeff Silver with BMO Capital Market.
Thanks so much. I know it's late, I will just ask one. Just continuing the conversation about inflationary increases. I'm just wondering from an M&A perspective, are your sellers’ expectations also increasing it, are they're either expecting higher multiple? Or are they talking about adjustments to adjusted EBITDA because it'll be higher cost? Thanks.
I guess anecdotally, what I would say is we have heard that sellers are facing the same [Indiscernible] in the work placing which is -- and we've kind of called it the great resignation and so a lot of them are saying, I've had enough and I'm going to ahead and sell. But I will tell you this in terms of their expectations, I can't control their expectations, what I can control is what I pay. And I would much rather grow organically than pay a multiple of 13 or 14 times. We're going to continue to be disciplined about that.
Okay. That's great to hear. Thanks so much.
Your next question is from the line of Jerry Revich with Goldman Sachs.
Yes, hi. Good morning. Jim, in your prepared remarks, you mentioned some of the ten percentage points of price increase are needed to cover the higher costs, can you talk about open market price increases that you folks are putting through in October and into year-end? Are you seeing that 10% improvement at the yield line for your open market business based on price increases you're putting through now on what's up
for renewal?
Now that 7% to 10% is more of a core price number. I mean, that's the price increase that we're taking. So, in order to get down to yield, you have rollbacks and then there's a mix component in the yield calculation. So, you're not going to see 7% to 10% yield. But we do feel like with -- I mentioned that we've seen 8.7% labor inflation for the quarter. So, in order to cover 8.7% labor inflation and Devina and John talked a lot about the non-labor inflation that we're seeing. We do feel like we've got to take 7% to 10% price increase. So that's what that number is.
Okay. And I believe it was two quarters ago, maybe you mentioned that you're satisfied with the way the industry has priced rationally so far in this recovery, has that continued, and now that we're seeing this acute period of inflation?
Did I say that? I usually don't comment on the industry because I can't control the industry. But I am satisfied with how it worked, and we do a nice job of looking at not only what our inflation is, and this has been much more accelerated than we anticipated. But also, how do we -- how do we improve margins? And then -- and I think when you look at just about any metric, the one that we've -- we've held out as being a real success story is residential. with residential yield of 5%, it wasn't that long ago that we were talking about residential yield in kind of the 1% range, we feel good about our own lines of business in terms of our own pricing. And that's really the only place that I speak of is what WM is doing.
Okay. And then in terms of -- on the labor costs topic, obviously labor availability is going to be low for the duration of this economic cycle. So, what gives you comfort that we've reached that point of peak inflation from a training cost standpoint, etc., if labor availability could actually be an escalating issue if we're having this conversation a year from now.
Well, I think Jerry, we've obviously got in front of the wage adjustments. We started that a couple of quarters ago, really in Q2, and I think that's certainly helped the other benefits we have in place have certainly helped. And I think we're tracking the job openings obviously versus volume. And the good news is the volume is still strong. That does put some pressure on the folks that we need to recruit. But as I mentioned, for the last 4 or 5 months, we're making headway in terms of what we have versus what we need, even relative to that volume.
And I don't think we can overstate it, I've talked about it a number of times, but a lot of conversation of pricing today has been the primary lever. But I don't think we can overstate the importance of using automation to take some of the labor intensity out of this business. It's a very labor-intensive business. We have positions that have very high turnover that does not imply that we're going to come out with a big reduction, that's not what I'm saying. I'm saying we can automate some of these roles and then use the attrition to our benefit.
I appreciate the discussions. Thanks.
Take care.
Your next question is from the line of Michael Feniger with Bank of America.
Hey guys, thanks for squeezing me in. I'll keep it short. Just for free cash flow conversion, Devina, when we think about next year, can you just walk through the puts and takes, obviously, CapEx this year is coming a low-end for obvious reasons. There might be some catch-up next year so maybe CapEx of sales higher-than-normal. But maybe you could walk through, we think about next year 2022 the working capital taxes, anything you'd like to highlight, as we're thinking about 2022.
Yeah. That's great question, Michael, and we're certainly already looking at how then to do it, a 2022 outlook. The strong conversion in 2021, we step back from that and say if we're targeting a conversion of every EBITDA dollar check free cash flow at 50%, we think that that's the outcome that's representative of a long-term trend for our business. We've had success reducing our interest in tax cost, tax as you mentioned, could be a question mark for the year ahead.
Too early for us to say one way or the other although we are optimistic based on some of the conversations that are happening currently. The progress that we've made on working capital management has been really strong. That's one where I would tell you it's too early for us to declare victory. We're implementing new systems and processes and those are showing some value. But it's certainly difficult to use that at least above that 50% target. In terms of managing Capex, that really is the one that we're focused on. Because for us, a capital dollar really should be looked at no differently than an M&A dollar.
And if we can get a better return on invested capital from accelerating capital in our recycling business or renewable energy facilities, we're going to do that, and so while we're going to look for opportunities to accelerate capital, we're going to do so in the same prudent way that we always do from a capital allocation perspective. And look at long-term maintenance capital versus what we will consider more of a growth-oriented or investment-oriented capital decision. So that's the one place that there could be an evolution in our discussion in 2022, but no specific outlook that we can provide at this point, we'll give you more color next quarter.
That makes sense. And since you mentioned 2022, when I look at the midpoint of your 2021 guide, implies a margin of 28.3%, around there. That's kind of the fourth straight year of being in that margin range. Now, granted one of those years was in a pandemic, so that's impressive and now we're contending with inflation. So, I know this has been asked a couple of different ways, but do we think that the margin, the typical margin expansion we see in this business, 50 bps or so. Is that more of like a 2023 story, as we're kind of in the odd period of coming out of COVID and deal with some of these inflationary pressures?
What's really interesting in that same three-year period that you mentioned is the impact of recycling on our margin. And I think if you stripped out a way and really consider the inflationary cost impact and the COVID impacts that we've already discussed. You are seeing strong execution on the front line of delivering that 50 basis points of margin expansion. That's why we really wanted to add the color on commodity price impact in the press release, so hopefully you can take a look at that table.
But I do think that, when we look at the collection efficiency at all of these training impacts, we've been really satisfied with the continued front-line execution of the team in delivering margin expansion though it is covered up. So, we have positive expectations for 2022 at this point though there is going to be some continued noise from the recycling part of the business.
Great. Thank you.
Thanks Michael.
Thank you.
And there are no further questions at this time. I will turn the call over to Mr. Jim Fish, President and CEO.
Well, just to conclude, thank you to -- again, big shout out to all of our 50,000 folks for the great quarter. This has been a challenging year and a-half challenging two years for everyone, but particularly for them who have been providing essential service on the frontline since day one. So, thank you to them. Thank you to all you for joining us this morning. We look forward to talking to you through the quarter and early in next year. Thank you.
This concludes today's conference call. Thank you for participating. You may now disconnect.